Interview with Phil Lawrence - Owner/GM
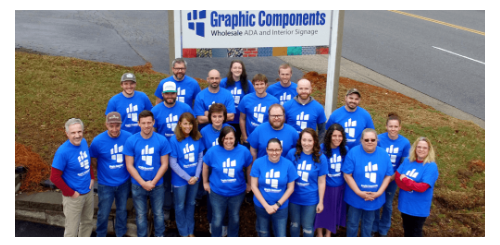
1. How long has your business been in operation and how many current employees do you have?
Graphic Components has been open since 2006 and we currently have over 20 employees.
2. Can you tell us a little about what your business does?
Graphic Components is a wholesale only fabricator of ADA and Interior Signage for Sign Companies and not resellers. We focus on superior customer service, quick turnarounds on quote requests, as well as shipping orders complete and on-time so our customers don’t have to spend time worrying about getting the job done. We maintain a very low overhead so that we can offer very competitive prices. We have been designated as one of two, Wholesale Only Preferred Fabricators of Photopolymer signage by Nova Polymers. Many of the largest Sign Companies in the U.S. are our customers.
3. What is your educational and/or business background?
I went to school for Graphic Design at the University of North Carolina at Greensboro and then managed a printing company before going into the sign industry. A lot of the similar business principles apply to both trades.
4. Can you please explain how you found MultiCam?
We knew we could improve our efficiency quite a bit by having a new router. We compared the competition to MultiCam and a big advantages (for MultiCam) was the service side of it. Having the ability to talk with service technicians and diagnose problems before having them come onsite was a big plus. We were also actually able to go to Charlotte, NC and see one of the machines in action and bring back test pieces. Really, the MultiCam had everything we were looking for – specifically the multi-tool changer and the camera registration. We fabricate really small parts and pieces so we needed a very strong vacuum and the vacuum that was sold with the system got the job done. We were afraid a robust machine wouldn’t be able to handle the small pieces we needed but we very pleasantly surprised we were able to cut those pieces accurately.
5. What type of MultiCam machine(s) do you currently own and how long have you owned it?
We currently own an APEX3R CNC Router and have had it since September of 2017
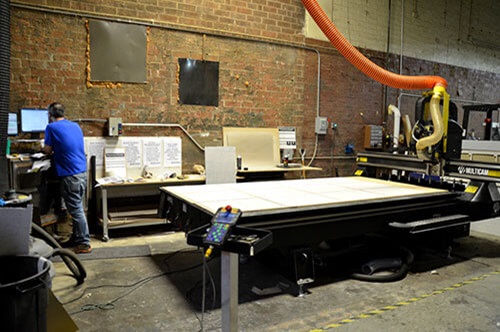
6. What do you like most about the MultiCam machine and what makes it the right choice for your applications? Approximately how much time did it save you?
We used to do routing manually/painstakingly versus being able to incorporate the camera registration into a lot of our processes. Now we’re able to add/print registration dots to the art work so we don’t have to worry about keeping the sheets square. The camera itself automatically squares the sheet on the table and cuts it very accurately. Basically, we’ve been able to save a lot of time by using the camera and automatic multi-tool changer whereas on the old router we had to change bits manually between each different path we wanted to do. I would almost guarantee we spend 50% less time routing our pieces with the APEX3R CNC Router from the process we used to do before.
7. Approximately, how many hours does the MultiCam machine run per week?
Our APEX3R CNC Router is typically on a 40 hour work schedule.
8. What type of material(s) and/or parts do you frequently cut?
Especially for the MultiCam Router we cut a lot ADA compliant signage and architectural interior signage (i.e. apartment and hospital signage) out of acrylic, aluminum, PVC, HDU, and photopolymer.
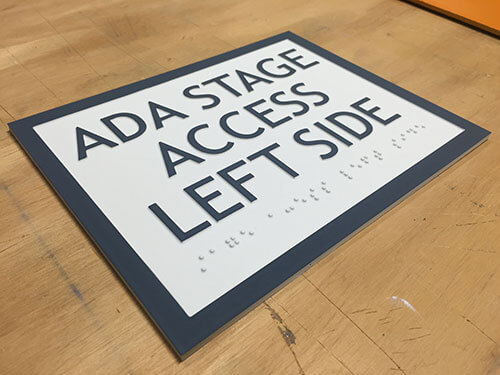
9. How has incorporating a MultiCam machine improved your workflow?
We do a lot of edge profiles such as simple bevel, a step, or a round over which we used to do manually but with the automatic multi-tool changer we have been able to streamline processes which involve multiple bits at different depths to achieve a much more ornate product at a fast production setting.
10. Is there any reasons why you chose a MultiCam machine over a different CNC provider?
The price was very fair, there were cheaper alternatives but they weren’t going to come with the quality that we felt we were getting with a MultiCam. Also, since we are a wholesale only company and work with so many other companies, we were able to reach out to them and get their experience on working with a MultiCam machine.
There was especially one job that one of our customers sent to us to produce for them – they sent us some samples that they produce themselves on their MultiCam and it was unbelieve what they were able to do compared to the Router we were using at the time. So we asked them specifically what brand and model they were using and they recommended MultiCam.
11. Can you describe any advantages you see choosing a MultiCam machine?
The big thing was the solid state of the chassis. Also, the maximum depth feature helps you prevent from making errors versus a lot of other machines that go deeper than what the project calls for. There are fail safes that MultiCam has in place to keep the operator from making an expensive mistake.
12. Would you like to add any additional comments?
Gabe, the service tech out of Charlotte, NC has been a great resource and representative of MultiCam as he helps with any problems we may have. He has help solved some of our specific problems to get us back on track.